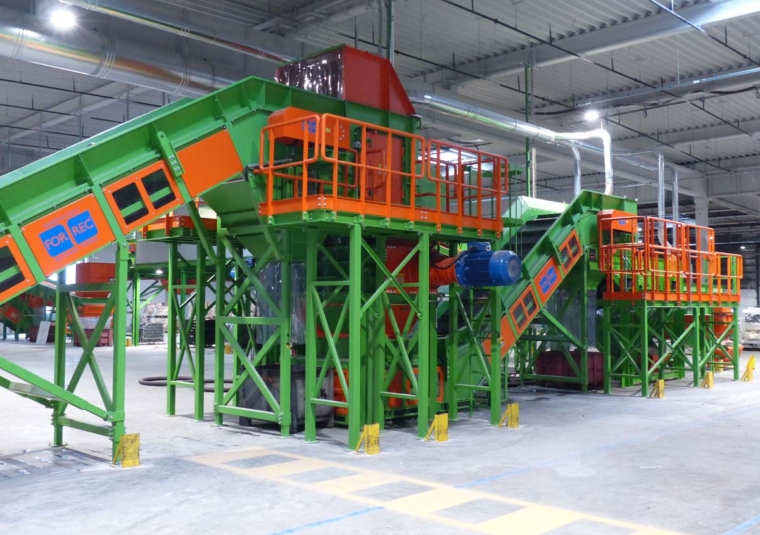
How to recycle a refrigerator: the treatment of dangerous WEEE
15 years: this is the average lifetime of a refrigerator or freezer. Once disused, this product must be recycled properly. For the treatment and disposal of refrigerators, therefore, specific technologies must be used, capable of treating not only their solid components, but also any oils and gases they contain that are harmful to the atmosphere, such as CFCs or HCFCs, or that have a high level of flammability, such as Pentane.
FOR REC has distinguished itself, in recent years, for the design and production of complete lines for the treatment of refrigerators, with tailor-made technologies developed and realized for European and non-European markets. Let’s see the main steps for the treatment of refrigerators according to FOR REC technologies.
120 refrigerators per hour treated with a single line
The lines designed by FOR REC engineers for the treatment of refrigerators (classified as WEEE R1 waste) are distinguished by
- input volumes: the highest in the world treated by a single line;
- the high efficiency in the recovery of gases such as Pentane and CFC: which allows these systems to fall within the WEEELABEX directives (the strict and extremely detailed European standards for the management of WEEE – Waste Electrical and Electronic Equipment).
The WEEELABEX regulations have defined, in particular, limits for emissions, registration of treatments and level of cleanliness of the treated product at the output. All FOR REC plants comply with the WEEELABEX regulation, which requires for all incoming refrigerators the cataloguing, weighing and classification according to size (small, medium and large), type and charge (CFC, cyclopentane and pentane).
How is a disused refrigerator treated? Key steps for recycling
The treatment of refrigerators in the FOR REC plants follows certain steps, let’s see them in detail:
1) Pre-treatment: in this first phase the refrigerator is weighed and prepared to be introduced into the processing line. This is a manual operation that consists in the separation of specific components such as: lamps, glass shelves, electronic boards and wooden parts.
2) Securing or recovery of refrigerant circuits: the refrigerator arrives at the emptying station, where the compressor and the refrigerant circuit are prepared for suction and subsequent separation of the gases and oils contained. Then the compressor and the refrigerant circuit are also removed and their disposal and recycling is managed separately.
3) Automated treatment of the plant: the refrigerator enters a shredding tower and is subjected in sequence to the action of two different types of shredders, to obtain a homogeneous size of the material. In this phase specific machines reduce it into pieces with dimensions between 40 and 60 mm and pulverize the polyurethane. This is followed by a phase of metal separation and subsequent granulation of the product, so that all the different elements present in the small pieces (aluminum, iron, plastic, copper and polyurethane) are separated thanks to operations carried out in sequence with precise instruments: zig-zag separators for the polyurethane, magnetic separators for the iron, densimetric separators for all the other components. The polyurethane usually keeps some traces of gas inside, so it is sent to a pressing system, to become inert and then be safely transported to its final destination.
All these operations are carried out in a controlled atmosphere and with high-tech safety systems, in order to avoid that polluting gases are dispersed in the environment or that there are excessive concentrations of gas in the most dangerous areas or, finally, to intercept gaseous mixtures.
4) Subsequent treatment phases
These phases are completed by a state-of-the-art system for the treatment, with different technologies, of the gas contained in the polyurethane foams used as insulation material in refrigerators. The output materials can be reused and put back on the market as secondary raw material.